Some Known Details About Alcast Company
Table of ContentsThe Buzz on Alcast CompanyAlcast Company Fundamentals ExplainedThe Best Strategy To Use For Alcast CompanyAlcast Company - The FactsThe Best Strategy To Use For Alcast CompanyThe Greatest Guide To Alcast Company
The subtle difference hinges on the chemical web content. Chemical Comparison of Cast Light weight aluminum Alloys Silicon promotes castability by reducing the alloy's melting temperature and enhancing fluidity throughout casting. It plays a vital duty in permitting complex molds to be filled accurately. In addition, silicon adds to the alloy's toughness and wear resistance, making it useful in applications where resilience is vital, such as vehicle components and engine components.It additionally boosts the machinability of the alloy, making it much easier to refine into completed products. By doing this, iron adds to the general workability of light weight aluminum alloys. Copper increases electrical conductivity, making it useful in electric applications. It additionally boosts corrosion resistance and adds to the alloy's overall strength.
Manganese adds to the toughness of aluminum alloys and improves workability. Magnesium is a lightweight component that supplies strength and influence resistance to light weight aluminum alloys.
The Basic Principles Of Alcast Company
It enables the production of lightweight elements with outstanding mechanical residential properties. Zinc improves the castability of aluminum alloys and assists regulate the solidification procedure during casting. It improves the alloy's stamina and firmness. It is typically discovered in applications where complex forms and fine information are needed, such as decorative castings and specific automotive parts.
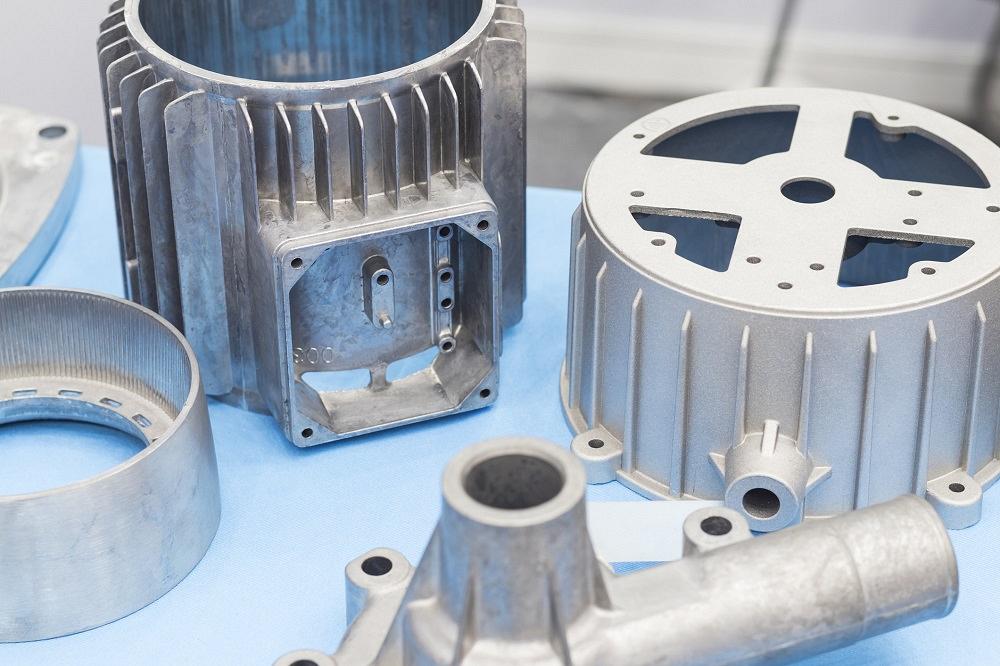
The key thermal conductivity, tensile toughness, return strength, and elongation differ. Select appropriate raw products according to the efficiency of the target product generated. Amongst the above alloys, A356 has the highest possible thermal conductivity, and A380 and ADC12 have the least expensive. The tensile restriction is the contrary. A360 has the very best yield stamina and the greatest elongation price.
The Of Alcast Company

In precision spreading, 6063 is well-suited for applications where complex geometries and top notch surface area finishes are critical. Instances include telecommunication units, where the alloy's superior formability permits for sleek and visually pleasing designs while keeping my response architectural integrity. In the Lights Solutions industry, precision-cast 6063 components create sophisticated and efficient lighting components that call for detailed forms and good thermal efficiency.
The A360 shows premium prolongation, making it excellent for facility and thin-walled parts. In accuracy spreading applications, A360 is fit for sectors such as Consumer Electronics, Telecommunication, and Power Devices.
The Buzz on Alcast Company
Its distinct residential properties make A360 an important choice for precision casting in these industries, enhancing product sturdiness and quality. Aluminum Casting. Aluminum alloy 380, or A380, is an extensively made use of spreading alloy with numerous unique features.
In accuracy casting, aluminum 413 shines in the Customer Electronics and Power Tools sectors. This alloy's remarkable rust resistance makes it a superb selection for outdoor applications, ensuring lasting, durable items in the mentioned markets.
All About Alcast Company
The light weight aluminum alloy you pick will significantly impact both the casting procedure and the homes of the final product. Since of this, you should make your choice thoroughly and take an informed approach.
Identifying the most appropriate light weight aluminum alloy for your application will certainly indicate evaluating a large array of qualities. The initial group addresses alloy features that affect the manufacturing process.
Unknown Facts About Alcast Company
The alloy you choose for die casting directly impacts several aspects of the casting procedure, like how easy the alloy is to collaborate with and if it is susceptible to casting problems. Hot cracking, also referred to as solidification cracking, is a typical die spreading flaw for light weight aluminum alloys that can result in internal or surface-level rips or fractures.
Specific aluminum alloys are more prone to warm breaking than others, and your option must consider this. Another common flaw discovered in the die casting of light weight aluminum is pass away soldering, which is when the actors stays with the die walls and makes ejection challenging. It can damage both the actors and the die, so you ought to look for alloys with high anti-soldering homes.
Corrosion resistance, which is already a noteworthy characteristic of aluminum, can vary significantly from alloy to alloy and is a vital characteristic to consider depending upon the environmental conditions your item will be revealed to (Aluminum Castings). Use resistance is an additional property typically sought in light weight aluminum items and can distinguish some alloys